From Earth to Space: FPGA-Based Satellite Processing with Frontgrade + Lattice
By Tim Meade, Systems Design Engineer, Frontgrade
The space electronics industry is evolving quickly to meet the requirements of a complex, globally competitive world. New and legacy aerospace manufacturers alike are shedding the long-held practice of designing customized components in small volumes and instead are adopting purpose-built, commercial technologies. The shift is moving the space electronics industry from a bespoke model to one that more closely resembles the terrestrial defense sector.
The trend toward commercial off-the-shelf (COTS) technology is driven largely by the advent of constellation satellites that are defined by lower orbits and shorter missions. Low-Earth Orbit (LEO) and Medium-Earth Orbit (MEO) constellations that provide space-based distributed processing require a higher degree of asset redundancy in the event one or more satellites fail or fall offline. Whether it’s a military or science-based mission, the introduction of Artificial Intelligence (AI) is also on the rise and is driving the demand for data collection, processing and distribution across everything from satellite communications and climate science research to navigational aid and target acquisition.
The introduction of AI requires a level of processing, storage and connectivity that more closely resembles today’s advanced commercial electronics. At the same time, size, weight and power plus cost (SWaP-C) considerations have never been more critical given the need to launch and maintain satellite arrays for telecommunications, internet and emerging, space-based military C4ISR applications.
These evolving mission objectives require new approaches to re-programmability, scalability and re-use that are best served through the use of Field Programmable Gate Arrays, or FPGAs, and software-defined instruments. Commercial FPGAs are better suited to the space industry’s rapidly shrinking development cycles and the need to squeeze more payloads into smaller form factors.
The challenge is that FPGAs have generally missed the mark in terms of SWaP-C and performance parameters required for satellite applications. To date, the stark choice has been between large, expensive premium FPGAs that can cost as much as $200,000 each, or small FPGAs or microcontrollers with extremely limited bandwidth and processing capability that can perform simple functions, but are not able to serve as the main “brain” of the satellite.
This is especially problematic as the satellite industry takes a page from the commercial arena by moving from centralized to distributed processing, which requires that intelligence be designed where needed – at the edge or next to the sensor. These platform-like satellites require a common, reusable set of building blocks with robust digital and analog processing capability to pull real-world data from the sensors while retaining a small footprint and low power.
This need led Frontgrade (formerly CAES) to partner with Lattice Semiconductor for a solution. With nearly forty years of FPGA industry heritage, Lattice is the low-power programmable device leader and the largest provider of FPGAs in the industry by volume. This strong history of innovation includes over twenty years of proven reliability supplying to critical infrastructure such as the automotive industry. By enabling distributed processing systems in edge applications on Earth, Lattice is well positioned to partner with radiation hardening expert Frontgrade to tackle the same challenges in space. This includes Frontgrade's use of temperature-resistant tin-lead (SnPb) terminations and fully-depleted silicon-on-insulator (FD-SOI) technology that is inherently radiation-tolerant and greatly reduces single event upsets (SEUs).
Combining space heritage and FPGA domain knowledge, Frontgrade and Lattice are filling the gap between small and large processors with purpose-built Certus™-NX-RT and CertusPro™-NX-RT FPGAs. Designed by Lattice, these scalable, multi-functional, reusable processing building blocks are optimized for efficient distributed processing systems. Frontgrade's expertise adds critical space-flight assurance required for harsh environments, as well as single, traceable wafer lots that have passed radiation acceptance testing.
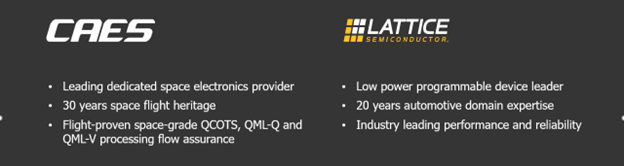
In addition to scaling its programmable logic fabric for CertusPro-NX, Lattice broadened the platform’s AI capabilities with easy to use tools, intellectual property (IP) and software required to innovate. Using the optimized signal processing blocks and 7.3Mb of internal memory, customers can load compact neural networks that enable multimodal intelligent sensing capabilities.
Frontgrade's fault-tolerant GR library (GRLIB) seamlessly complements Lattice’s Propel library and Radiant debug and design tools to offer an easy, intuitive and versatile design experience. Combined, these IP libraries deliver a holistic design environment for space engineers seeking to quickly create high-performance, high-reliability space processing solutions. Additionally, Frontgrade radiation and Lattice FPGA specialists can guide customers through the design process, acting as seamless extensions to customer in-house capabilities.
Global pace systems are adopting distributed processing architectures to build in more scalable performance and higher reliability. These architectures reuse common technology building blocks to reduce development time and program risk. Until now, space programs had small or large FPGAs to choose between which either under- or over-delivered. Our new FPGAs meet the needs of distributed space architectures by delivering mission-matched scalable performance for efficient, system-wide technology reuse.
Click to learn more about Frontgrade + Lattice, FPGAs and Frontgrade’s radiation hardened capabilities.